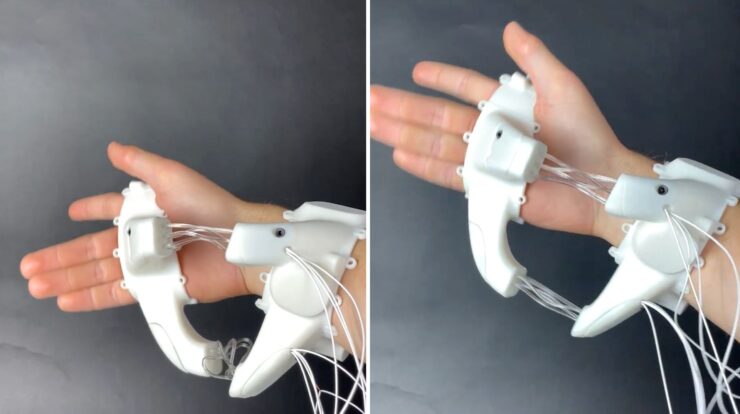
Scientists from Carnegie Mellon University (CMU) have created a sophisticated new algorithm capable of designing adjustable metastructures possessing variable rigidity along with all six degrees of freedom (DoF).
This advancement enables creators to embed intricate movement paths directly within materials, providing unparalleled command over the operation of joints in sophisticated mechanical setups.
The algorithm analyzes various kinetic setups, facilitating the creation of flexible machinery for different uses.
To showcase its capabilities, the team developed various wearable designs tailored specifically for different movements and areas of the body. This advancement has the potential to impact fields such as robotics, prosthetics, aerospace engineering, and wearable tech.
Next-gen haptic design
Systems featuring adjustable mechanics and variable rigidity are crucial for uses in virtual touch feedback, efficiency enhancement, and therapeutic recovery.
Previous research has examined stiffness-reconfigurable mechanisms utilizing electromagnetic, electrostatic, or pneumatic systems; however, these approaches frequently constrain the degrees of freedom because of their intricate mechanics. In contrast, compliant structures employing engineered materials present another option. Nonetheless, many such designs are limited to two-state operation and operate within narrow stiffness spans.
To overcome the shortcomings of earlier designs, researchers at Carnegie Mellon University improved the screw algebra-based Freedom and Constraint Topology (FACT).
model
To facilitate multi-modal adjustments while integrating characteristics such as bar rigidity and potential folding. This approach enables dynamic movement regulation across all six degrees of freedom, featuring adjustable firmness and adaptable structures tailored for different uses, particularly wearables.
At the heart of this method lies an enhanced design framework aimed at identifying ideal positions for flexural rods across various movement patterns. This technique merges theoretical models with finite element simulations to assess and improve effectiveness, leading to adjustable mechanisms customized for particular motion and structural needs.
The researchers built three sample devices to show how their system works. One is a wrist device that can change its stiffness, helping control how freely the wrist moves. Another is a fingertip “thimble” that can switch between soft and firm settings, simulating the feel of different materials like
gel
or metal. The third is a wearable made of several joints designed for the arm and hand, which can enhance touch feedback or assist with muscle training.
Adaptive motion control
In these systems, the stiffness-adjustable rods use electrothermal activation through heating wires. Although they work well, the metal wires’ restricted flexibility confines movement primarily to compression along the rod’s length.
According to researchers, this limitation might be overcome by replacing the heating wires with electrothermal epoxy materials, such as carbon nanotube-infused resin, potentially enabling bidirectional motion without added mechanical complexity. The stiffness contrast between locked and unlocked states may also be improved by such changes. However, particularly for high-precision applications, problems such epoxy hysteresis need to be addressed.
When heated to about 54 °C, these rods can also regain their previous shape, demonstrating shape-memory capability, but the efficiency of recovery varies depending on the type of deformation. In wearable settings, passive rods and user support can help with recovery even further. The system’s comparatively poor mode-switching speed as a result of passive cooling and joule heating is one of its disadvantages.
Although this approach restricts usage in high-speed scenarios such as gaming, it still proves effective for activities that can accommodate sporadic transitions, including motor skill therapy and work-oriented tactile feedback systems. Further studies could explore incorporating dynamic thermoelectric components or enhancing heat control strategies to decrease changeover durations.
Research suggests that these design concepts could potentially be applied to various other bodily regions and integrated with computers for enhanced training, mixed reality applications, or personalized assistance, alongside wearable devices for the upper limbs. To ensure broad adoption, refining the designs for comfort and effectiveness will be essential, along with employing scalable digital manufacturing methods such as embedding technology.
epoxy
printing may streamline production.
The specifics of the team’s
research
were released in the journal
Nature Communications.