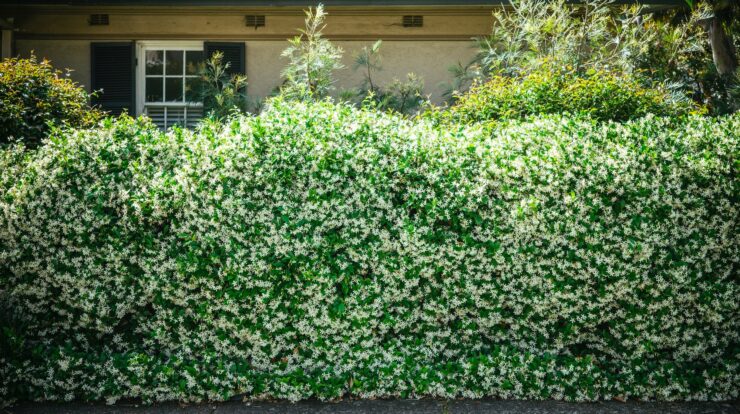
Scientists from Oak Ridge National Laboratory (ORNL) located in Tennessee have developed an innovative vacuum-assisted extrusion technique aimed at substantially decreasing internal voids within big-sized 3D-printed polymer components.
This advancement, according to the team, has the capability to revolutionize additive manufacturing within the aerospace, automotive, and defense industries by reducing porosity by 75 percent. This marks an important move towards producing stronger and more dependable printed parts.
Large-format additive manufacturing (LFAM), which offers a broader perspective on 3D printing, allows for the production of massive, intricate pieces measuring up to meters in size. This technique is utilized across multiple sectors to fabricate sizable, complex components.
Despite offering outstanding rigidity and minimal thermal expansion, these materials have not seen extensive usage due to internal porosity or cavities, which weaken and undermine the durability of the fabricated components.
Thanks to the latest vacuum-assisted method, scientists have succeeded in eliminating the gases captured during production, thereby considerably decreasing voids and enhancing part strength as well as consistency.
Understanding porosity defects
Vipin Kumar, PhD, specializes in composites and
fiber manufacturing
expert at ORNL, explained that even though 3D-printed materials provide excellent stiffness and low thermal expansion, their potential is greatly limited by persistent intrabead porosity.
In 3D printing, porosity denotes small cavities or imperfections inside the printed substance, typically resulting from
trapped gas
Or inadequate fusing during the printing procedure.
These vulnerabilities can function akin to minor cracks in glass, propagating under pressure and eventually undermining the integrity, robustness, and dependability of essential parts such as
medical implants
or aerospace parts.
To address the problem, the researchers incorporated a
vacu
um hopper
– a device used to remove air, moisture, and trapped gases from materials in manufacturing – directly to the
extrusion process
, where the material is warmed up and forced through a nozzle to create the printed component.
To their astonishment, the preliminary outcomes strongly underscored the method’s efficacy, showing a reduction in porosity of up to 75 percent, even in areas with differing characteristics.
fiber content
—a significant aspect of large-scale manufacturing where maintaining material consistency can be challenging.
Additionally, in certain instances, the internal void rate fell beneath two percent, a development that Kumar characterized as a substantial improvement over traditional techniques.
Reinventing polymer printing
Kumar stated that with this cutting-edge method, they are tackling the significant problem of porosity in big polymer prints and simultaneously setting the stage for more robust composite materials.
press release
.
The group proposed that incorporating the vacuum-assisted technique might smoothly fit within current LFAM processes, aiding in enhancing manufacturing efficiency and boosting component quality for industries such as aerospace, automotive, and defense.
“This represents a major advancement for the LFAM sector,” Kumar stated, elaborating on how the design efficiently removes gas from the material beforehand, guaranteeing a purer and more compact result.
As the system is presently configured for
batch based processing
The team is currently focusing on enhancing its abilities for ongoing, large-scale, and industrially robust uses.
They disclosed that they have already created a
patent pending concept
To incorporate the vacuum extrusion technique into ongoing deposition processes, which might propel this technology towards widespread adoption in contemporary, rapid-production settings.